Business
August 21, 2014
Unboxing MakerBot Replicator 2 for testing
Unbox and test the MakerBot Replicator 2. Explore its features and performance in this comprehensive review
Business
September 26, 2014
Maker Faire 2014 - The Greatest Show and Tell on Earth
Relive the excitement of Maker Faire 2014, the ultimate celebration of innovation and creativity, where makers from around the globe showcased their incredible inventions and projects.
Business
March 18, 2015
How To's : Navigating 3DPrinterOS
Master the art of navigating 3DPrinterOS with our comprehensive how-to guide. Start optimizing your printing experience!
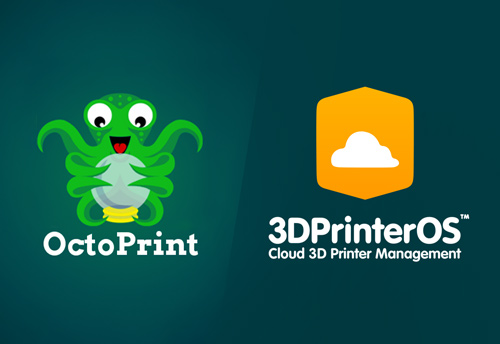
Advice
August 19, 2021
How to set up Octoprint easily with 3DPrinterOS. Octoprint partners with 3DPrinterOS.
How to set up Octoprint easily with 3DPrinterOS. Now You can easily log into 3DPrinterOS.com and the Octoprint Plug is easy to install and connect your 3D printer online, for remote control and easier access.
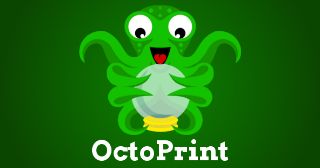
Business
August 18, 2021
How to set up Octoprint easily with 3DPrinterOS.
Discover easy OctoPrint setup with 3DPrinterOS. Streamline your 3D printing experience effortlessly.
Business
October 16, 2020
How to run socially distant 3D print projects
Learn how to manage socially distant 3D print projects efficiently with expert tips.
Insight
October 8, 2018
How to manage students, 3D printers and data at scale
Effortlessly manage students' 3D printers and data at scale with expert tips and insights.
Business
September 22, 2014
Enabling the future - Using your 3D Printer to make a difference
Empower the future with 3D printers. Discover how you can make a difference with the latest technology.
Insight
November 13, 2015
CEO John Dogru to speak at IDTechEx
Catch CEO John Dogru at IDTechEx, sharing insights on the future of 3D printing technology. Don't miss out!
Business
August 28, 2015
CEO John Dogru on the All Things 3D Podcast
Unlock insights into 3D printing with John Dogru. Dive deep into the world of additive manufacturing.
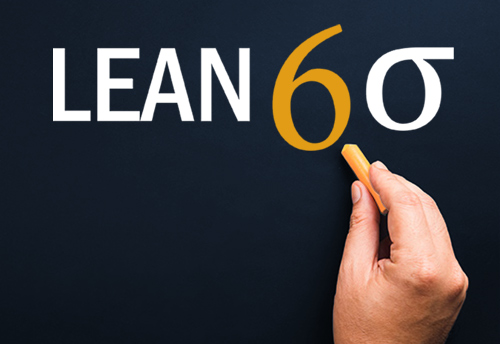
Business
July 28, 2021
Bockman’s Bites on Lean Six Sigma in Additive Manufacturing Part 1
Trim the fat. Cut your losses. Eliminate Muda.
Business
August 4, 2021
Bockman’s Bites on Lean Six Sigma in Additive Manufacturing Part 2
Delve into Bockman's insights on Lean Six Sigma in additive manufacturing - Part 2/5 of an enlightening series.
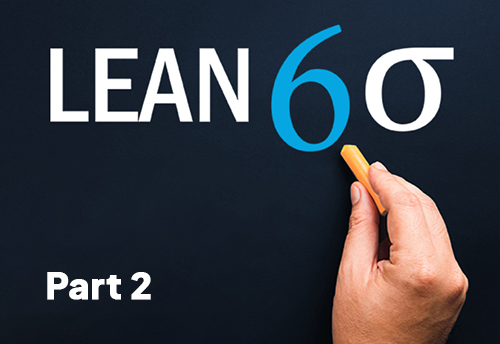
Innovation
August 4, 2021
Bockman’s Bites on Lean Six Sigma in Additive Manufacturing Part 2
I am writing a short series of bites about the importance of implementing Lean Six Sigma methodology in Additive Manufacturing... (Part 2)
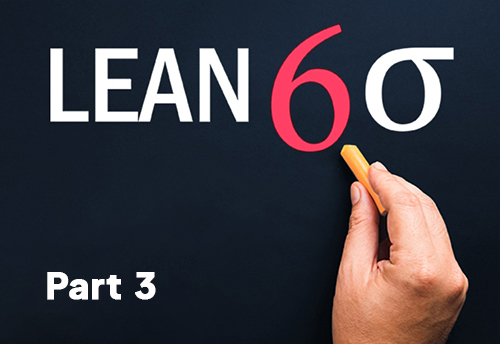
Innovation
August 12, 2021
Bockman’s Bites on Lean Six Sigma in Additive Manufacturing Last Chapter
I am writing a short series of bites about the importance of implementing Lean Six Sigma methodology in Additive Manufacturing... (Part 3)
Business
July 28, 2021
Bockman’s Bites on Lean Six Sigma in Additive Manufacturing
Discover Bockman's insights on Lean Six Sigma in additive manufacturing. Elevate your 3D printing process with expert guidance.

Insight
January 11, 2022
3DPrinterOS Founders Story, History of two devoted individuals (Part 3)
We examined the startup years of the company, and the passion that drives Dogru and Vedeshin, the cofounders of 3D Control Systems, to succeed. In this final chapter, we’ll dive deeper into the origins of these entrepreneurs.
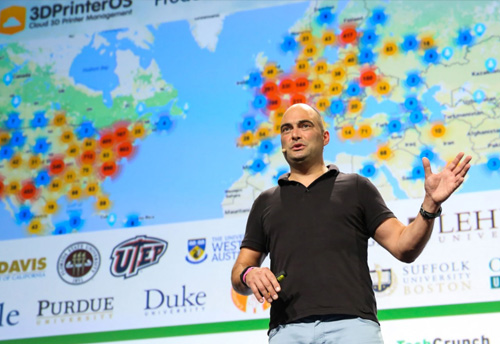
Insight
November 22, 2021
3DPrinterOS Founders Story, History of two devoted individuals (part 2)
Discover the inspiring journey of 3DPrintOS founders. Dive into the history of innovation and dedication!
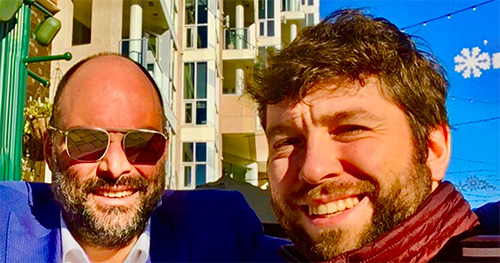
Insight
November 8, 2021
3DPrinterOS Founders Story, History of two devoted individuals (part 1)
Story about two individuals who are behind the achievement of 3D Control Systems are Mr. John Dogru and Mr. PhD. Anton Vedeshin
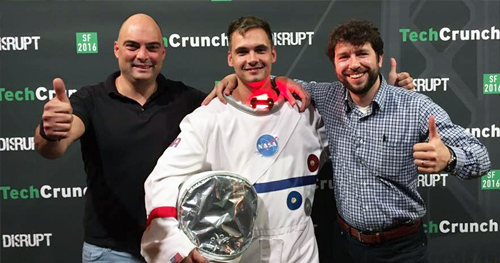
Insight
January 26, 2022
3DPrinterOS Founders Story, History of two devoted individuals (Last Chapter)
We examined the startup years of the company, and the passion that drives Dogru and Vedeshin, the co founders of 3D Control Systems, to succeed. In this final chapter, we’ll dive deeper into the origins of these entrepreneurs.
Business
December 3, 2021
3DPrinterOS Founders Story, History of two devoted individuals (part 1)
Explore the captivating journey of 3DPrinterOS founders, unraveling the history of their dedication - Part 1/5.
Business
January 27, 2022
3DPrinterOS Founders Story, History of two devoted individuals (Last Chapter)
Discover the inspiring journey of 3DPrinterOS founders, paving the way for innovation in 3D printing. Dive into their story now!
Business
October 22, 2014
3D Printed Food – Just as Good as the Real Deal?
Indulge in the taste of 3D printed food that's as good as the real deal. Explore the culinary revolution now!
Read our other posts
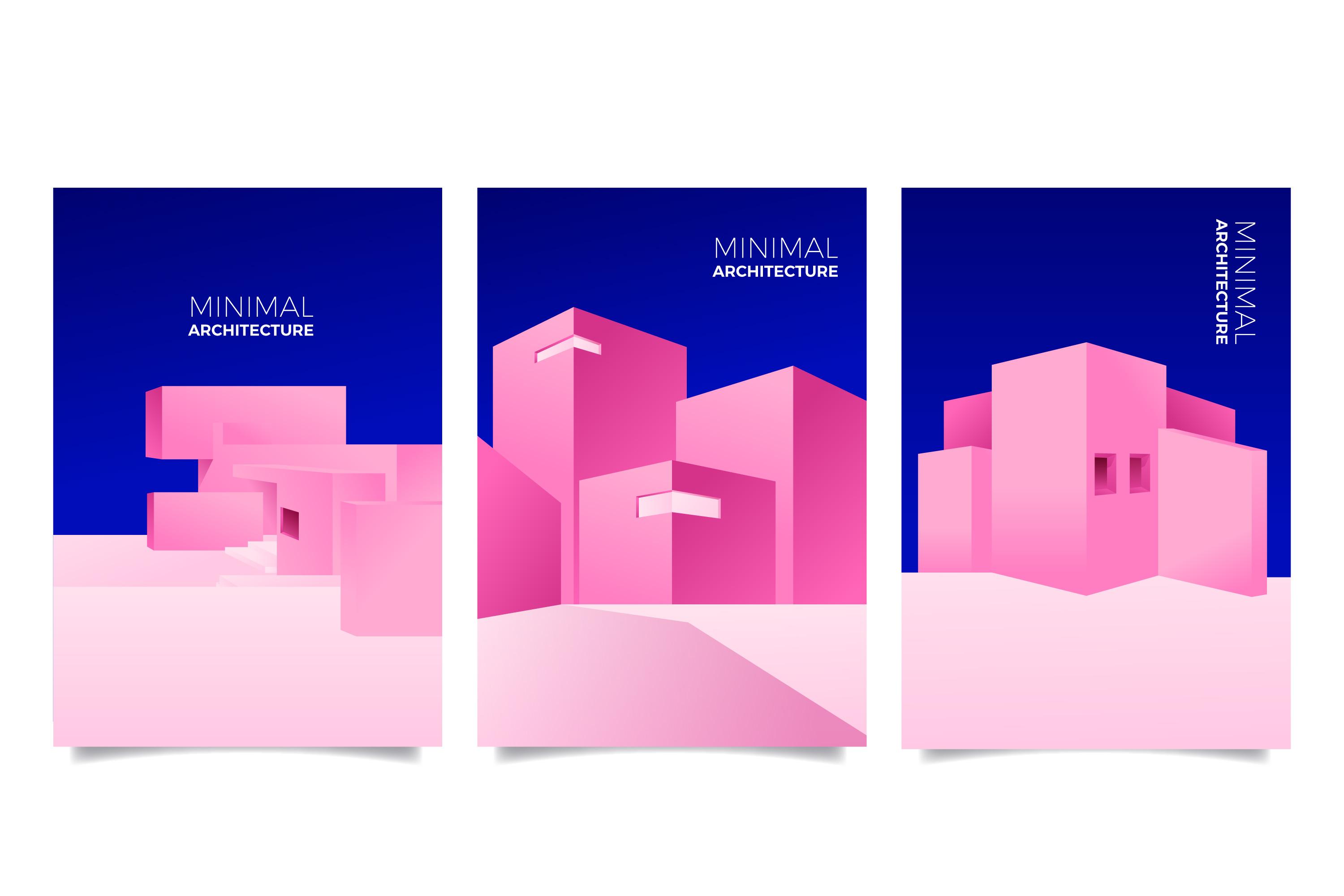
Innovation
February 16, 2023