Insight
July 21, 2021
The best workflow software for Fab-Labs and Makerspaces
Discover the ultimate workflow software for Fab-Labs and Makerspaces. Optimize your operations with the best solution available
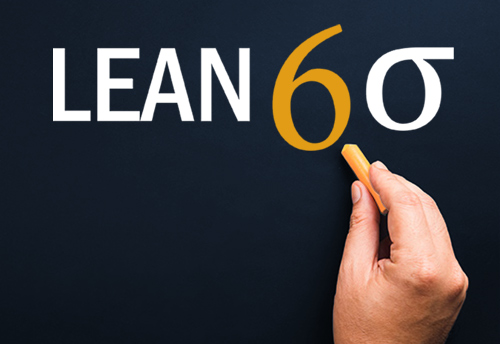
Business
July 28, 2021
Bockman’s Bites on Lean Six Sigma in Additive Manufacturing Part 1
Trim the fat. Cut your losses. Eliminate Muda.
Business
August 4, 2021
Bockman’s Bites on Lean Six Sigma in Additive Manufacturing Part 2
Delve into Bockman's insights on Lean Six Sigma in additive manufacturing - Part 2/5 of an enlightening series.
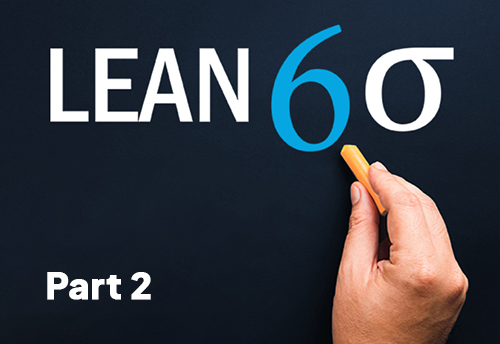
Innovation
August 4, 2021
Bockman’s Bites on Lean Six Sigma in Additive Manufacturing Part 2
I am writing a short series of bites about the importance of implementing Lean Six Sigma methodology in Additive Manufacturing... (Part 2)
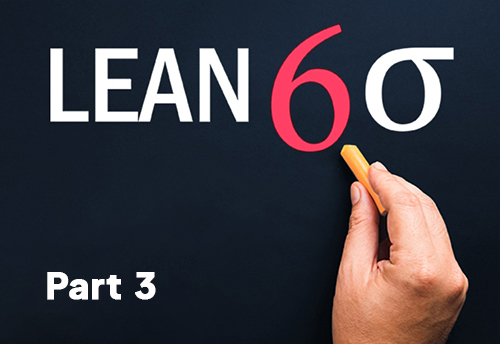
Innovation
August 12, 2021
Bockman’s Bites on Lean Six Sigma in Additive Manufacturing Last Chapter
I am writing a short series of bites about the importance of implementing Lean Six Sigma methodology in Additive Manufacturing... (Part 3)
Business
July 28, 2021
Bockman’s Bites on Lean Six Sigma in Additive Manufacturing
Discover Bockman's insights on Lean Six Sigma in additive manufacturing. Elevate your 3D printing process with expert guidance.
Read our other posts
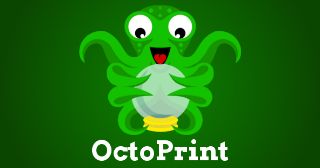
Insight
March 23, 2016
3DPrinterOS: Octoprint Alternatives
Business
March 18, 2015
How To's : Navigating 3DPrinterOS
Business
November 1, 2014
Alchemist Accelerator Secures backing from Siemens Corp.
Business
September 6, 2015