Revolutionizing the Automotive Industry: How 3D Printing, 3D Printed Parts, and Advanced Workflow Management Software are Transforming the Way Cars are Made
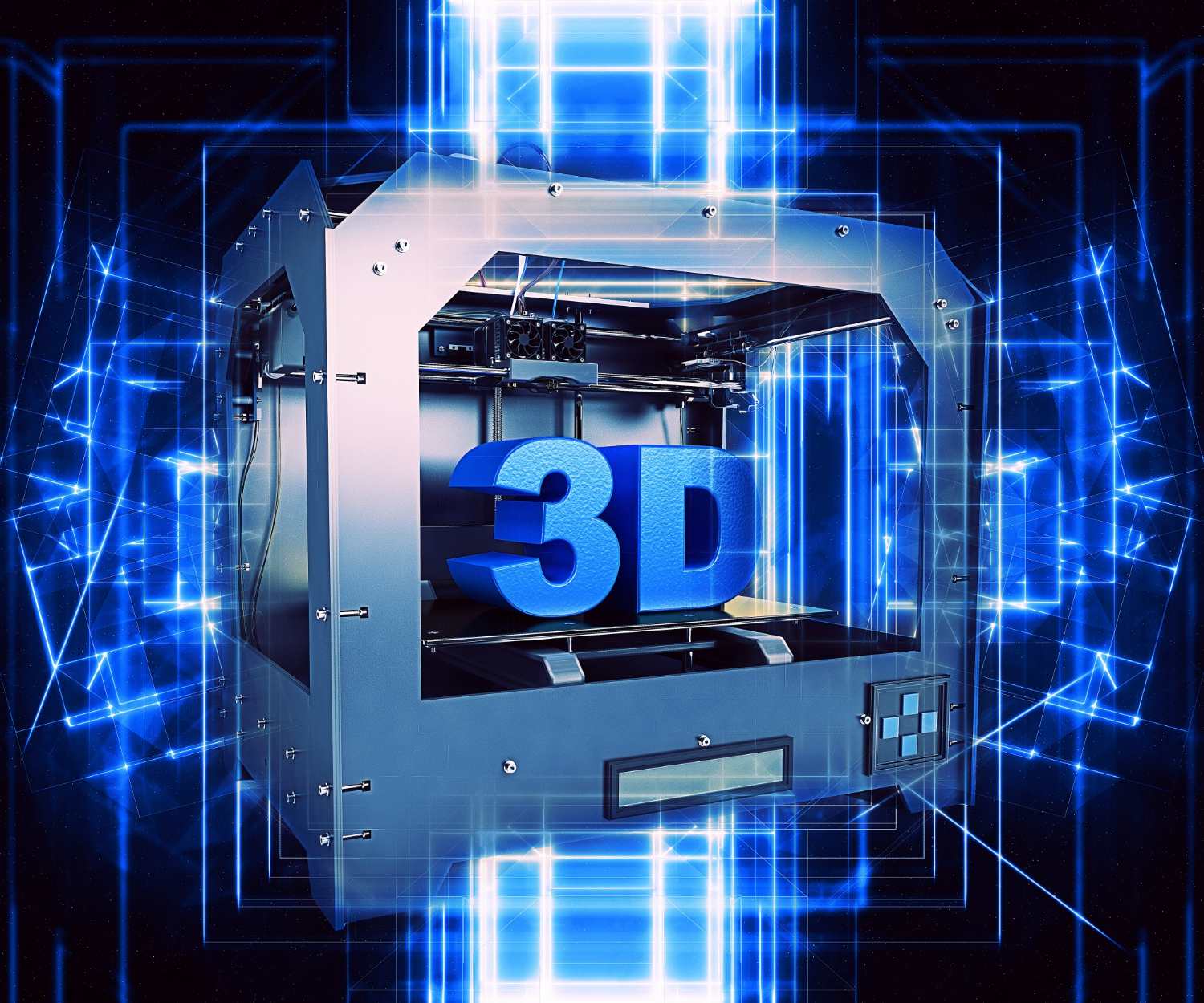
Three-dimensional printing, or additive manufacturing, is a process of making a three-dimensional object from a digital file. It is achieved using an additive process, where successive layers of material are laid down in different shapes. 3D printing has been used in the automotive industry for some time now, but it is only recently that its potential is being fully realized.
The use of 3D printing in the automotive industry is still in its infancy, but it has the potential to dramatically shift the way cars are made.
3D printing can be used to create complex parts and assemblies that would otherwise be difficult or impossible to manufacture using traditional methods.
One example of this is the lug nuts Ford is developing. Thanks to 3D printing they can be made with a pattern absolutely unique to the owner: a digital representation of the owner's voice as a soundwave pattern. They also make use of additive manufacturing's secret weapon - making use of hollows on the inside. In this case, the design widens as it gets deeper into the lug nut, which means a thief can't take wax impressions to replicate a key.
Automotive engineers are also turning to 3D printing as a way to solve complex heat exchange problems. To understand how beneficial additive manufacturing is in this case, you need to understand a little about traditional manufacturing methods: conventional technologies for making heat exchangers include milling, welding, casting, drilling, and welding or brazing. Interior channels are very limited in scope; both by the size and reach of the traditional tooling, and by the risk of leaking where flow-tight connections are required.
On the other hand, heat exchangers made with additive manufacturing allow for interior channels that curve and bend and turn corners, allowing a small outer size to still provide a large volume of channel flow.
Companies are able to use 3D printing to develop intricate and sturdy parts that were previously impossible, like complex chassis structures or plastic components with honeycomb details inside.
Not only that, but the ability to create iterations of these complex parts with 3D printing is a game-changer, compared to starting a piece over with traditional manufacturing. Where subtractive tooling design changes might traditionally be a multi-week process, additive allows design changes to be put into effect immediately.
We’ve seen the recent havoc played on the automotive supply chain. 3D printing can be used to produce custom parts on demand, which can greatly reduce lead times and inventory levels for carmakers.
The automotive industry is one of the most heavily regulated and highly competitive industries. With 3D printing, the supply chain in this sector can become more efficient and cost-effective. By allowing companies to build custom parts quickly and precisely within their own facility, 3D printing reduces lead times, minimizes inventory costs, and accelerates the production of new models.
By taking advantage of this technology, companies within the automotive industry can stay agile and foster innovation through short run custom parts that are quickly manufactured onsite. 3D printing allows for faster response to feedback from customers, which can result in increased efficiency throughout the entire supply chain.
3D printing also reduces costs associated with storage for replacement parts and shipping costs of those parts around the world.
The automotive industry is currently undergoing a period of dramatic change, and 3D printing will play a significant role in shaping its future. It will be interesting to see how this technology develops over the coming years and what impact it has on the way we build cars.
The ability to rapidly iterate a design, test it, and then quickly make improvements has made 3d printing attractive to the industry. The automotive industry has been rapidly evolving in recent years, and 3D printing is a major part of this transformation.
By enabling quick iterations of design, 3D printing has allowed the automotive industry to considerably reduce the time it takes to bring a product from concept to reality. Additionally, through 3D printing, companies are able to customize parts quickly and cost-effectively which helps them remain competitive on the global market.
With this booming technology driving innovation within the industry, it's safe to say that 3d printing is helping create a new standard for automotive design.
Additive manufacturing has also opened up an array of opportunities for customizing everything, from individual parts for cars to entire vehicle designs. Customers can tailor actual parts to their exact specifications rather than relying on off-the-shelf components offered by car manufacturers. Among other applications, this opens a new realm of possibilities for creating customized seats, dashboards, or other parts for people with disabilities.
Using 3D printing, individuals with particular needs can now design and manufacture custom car parts that are tailored to their requirements. This highly accessible and cost-effective technology is helping to make the dreams of a more personalized vehicle much closer for those with physical challenges. 3D printing has further enabled customers to get creative, giving those with mobility issues the freedom to create the perfect car part - there's no longer any need to worry about finding an off-the-shelf piece that may not fit properly or match their desired aesthetic.
Instead, 3D printing technology allows engineers and technical teams to turn CAD models into physical products quickly and efficiently, drastically shortening development times for custom automotive products. This means faster production delivery and cost savings for both the customer and manufacturer – a major win-win situation for all involved in the manufacturing process.
3D printing is already having a big impact on the car industry, and it is only going to become more ubiquitous in the future. 3D printed parts can be made lighter and stronger than traditional parts, and faster and more economically.
Learn more about 3DPrinterOS - the most trusted 3D printing management software for Higher Education, Enterprises and OEMs. Fill out this form to get in touch with our experts.
Manage the workflow and permissions for your users
Share files and 3D printers to groups of users
Control your 3D printer fleet through a browser
Cloud slicer and toolpath viewer
Book your personalized assessment now and get your free trial.