Bockman’s Bites on Lean Six Sigma in Additive Manufacturing Part 2
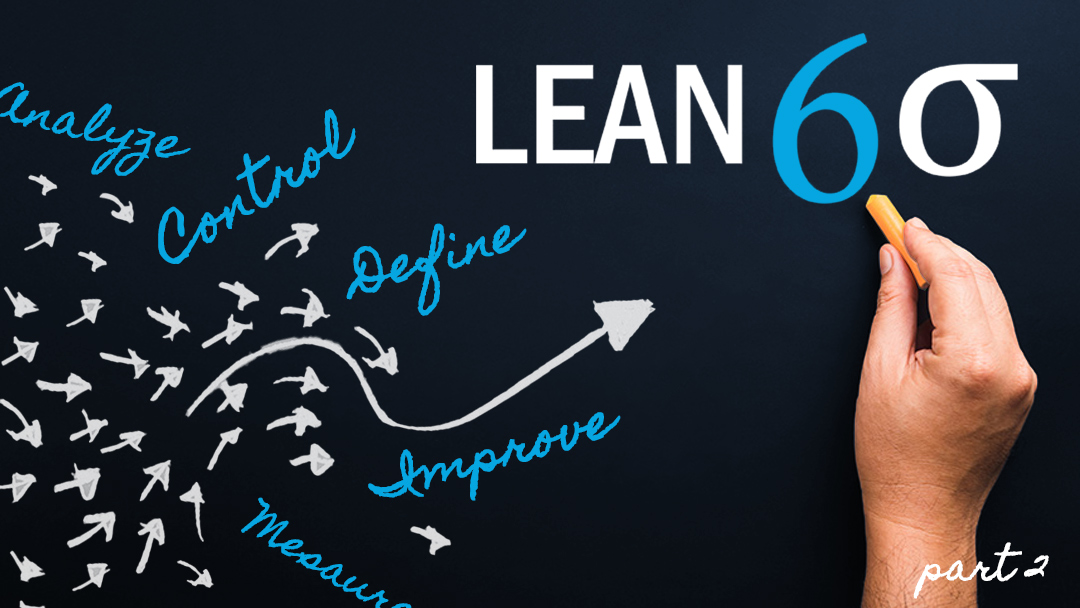
Welcome back to Bockman’s Bites … now, on to the second one...
I’ve decided now is not the time to discuss the benefits of additive manufacturing, but rather the challenges. While additive manufacturing has evolved for the past three decades, it’s still a relatively young industry, and we are beginning to see new hardware, software and material providers pop up everyday. It’s certainly an exciting time for AM enthusiasts, but it’s cumbersome for many commercial and industrial manufacturers who wish to maximize the advantages of AM. It introduces a lot of waste (muda) into the workflow that traditional manufacturing has conquered. In my estimation, these are the biggest challenges that L6S-AM can tackle. I witnessed it many times when I was visiting customers in automotive.
Combining with Conventional Manufacturing | How can AM be complementary to existing processes? For starters, designing with AM is unique compared to subtractive manufacturing and requires a different engineering mindset. In addition, most production facilities are unwilling to completely change their processes without understanding the time, quality or cost benefits associated with AM. This lack of knowledge and confidence leads to adoption hesitancy. How is the industry addressing it today?
Contract Manufacturing or Service Bureaus | Embracing new technologies and innovation comes with careful consideration for many machine shops and production facilities. The challenge is to find a complementary approach to manufacturing that seamlessly determines which technology is the most cost effective (or time sensitive) solution depending on the part or application. This is not easy considering the subtle design differences required to maximize each technology or material. For many machine shops and contract manufacturers, this connection may not exist which leads to poor utilization or worse, lack of technical understanding of the capabilities. How are manufacturers making it easier on themselves?
US Machine shops are oftentimes family owned businesses that have organically grown and adopted technologies as the business expands. They may have CNC, injection molding, tooling, sand casting, and additive manufacturing capabilities under one roof. A recent report suggests that 26% of major OEMs are already outsourcing parts to a contract manufacturer/service bureau and expect that number to increase year-over-year due to a variety of reasons. Machine shops are looking for a way to reduce the additive manufacturing process which tends to be super manual and labor intensive. Not to mention, contract manufacturers are without a software solution that can connect all the technologies which leads to cumbersome production, missed timelines or duplicated efforts. The anticipated growth forces many machine shops to identify a software platform that allows them to digitally view the production floor, assign projects, and proactively identify problems (failed builds, predictive maintenance, equipment downtime). Having an integrated software that aggregates data from these production processes will enable engineers to determine a cost/time analysis and get parts out the door faster and cheaper. The competition isn’t waiting, why should you?
Check back in next week to see how the L6S-AM is affecting the automotive and aviation industries.
Leveraging Equipment & Technical Expertise | Companies with multiple prototyping or production facilities are oftentimes handcuffed when it comes to optimizing technology capabilities. This is common for major OEM’s in aerospace, automotive and defense sectors that do not have access to partner facilities located in the US or elsewhere. We are beginning to see more OEM’s create AM Centers of Excellence, but it remains challenging for the entire organization to leverage resources and plan accordingly. L6S-AM is an important consideration because the bottlenecks associated with poor planning will result in wasteful spending or worse. Additive manufacturing machinery, like any major capital equipment expenditure—has a shelf life, and downtime is unacceptable.
Automotive & Aviation | Automotive and aviation manufacturers are notorious for having multiple production and final assembly plants strategically located throughout the globe. The technology at each site varies depending on a variety of reasons (expertise, access, proximity, etc.) but the glaring challenge is to leverage the right technology, for the right application, that provides maximum value to the organization. Too often, the different facilities do not communicate well enough and are completely blind to what is available for resources. There is no singular language or software platform that can seamlessly connect the departments and accurately monitor equipment or material inventory in real-time. Simply put, it’s a lack of resource utilization.
AM was originally destined to be a prototyping tool so OEMs never implemented lean practices that would enable the technology to be a true manufacturing alternative. While AM is revolutionary, many manufacturers are losing precision cycle time just waiting between queues.
Lufthansa Technik, a major supplier of maintenance, repair, and overhaul (MRO) services partnered with Oerlikon AM in 2018 to establish an AM Center dedicated to advancing the technology. The ability to produce one-off spare parts will cut costs significantly and improve lead times. Other manufacturers are adopting a similar strategy and beginning to centralize AM expertise while continuing to decentralize hardware capabilities, enabling on demand and localized production. With countless SKU’s, design standards, and testing data, it becomes challenging to aggregate this information for actionable purposes. Having an integrated software that combines data with production transparency will ultimately lead to better planning and less downtime.
Check back in next week to see how L6S-AM is affecting the medical market.
Data Transparency | AM introduces so many new technologies, materials, post processing requirements, pricing models and design considerations that it becomes dizzying. Not to mention, the industrial infancy of AM is a key contributor to the lack of standards available within the marketplace. How can engineers, scientists, doctors, and researchers maximize additive manufacturing without a proper execution system in place that can track, aggregate and monitor so many valuable data inputs? Without data or worse, inaccurate data, management is completely blind and unable to make process improvements. The medical market, well-known for its strict standards, embraces additive manufacturing but is still learning how to optimize it. Can a L6S approach help streamline additive manufacturing processes and improve efficiency?
AM has been tremendously beneficial to the development of personalized patient healthcare options. Custom treatments, prosthetics, surgery solutions, implants and more are now possible with additive manufacturing. However, implementing AM into a hospital setting compounds the challenge that already exists, too much data. Combining large, digital patient data with AM is a nightmare for most doctors and physicians. It’s cumbersome, complicated and inefficient.
Learn more about 3DPrinterOS - the most trusted 3D printing management software for Higher Education, Enterprises and OEMs. Fill out this form to get in touch with our experts.
Manage the workflow and permissions for your users
Share files and 3D printers to groups of users
Control your 3D printer fleet through a browser
Cloud slicer and toolpath viewer
Book your personalized assessment now and get your free trial.